A 3dpbm conversou recentemente com Jason Rolland, vice-presidente sênior de materiais da Carbon , sobre o desenvolvimento do EPU 44, um elastômero bioderivado, imprimível em 3D, com qualidades de aprimoramento de desempenho.
Desde o início, a Carbon queria fazer algo diferente no mundo da manufatura aditiva. Quando a empresa questionou por que a tecnologia não era usada mais amplamente na produção, a conclusão foi que dois problemas principais estavam causando essa falta de adoção – velocidade de impressão e materiais.
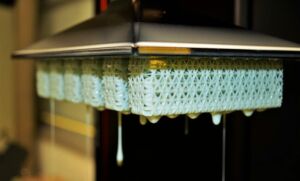
A velocidade de impressão foi importante para ser relevante o suficiente para a produção em indústrias como a de calçados, onde a velocidade de fabricação afeta significativamente os custos finais do produto.
Com relação aos materiais, o problema era, especificamente, “em torno da seleção de materiais em relação ao que as pessoas fariam com as tecnologias de moldagem. Com espumas, por exemplo, em particular com elastômeros, havia muito poucas tecnologias relevantes para elastômeros e impressão 3D, e muito trabalho foi necessário para chegar ao ponto em que você pudesse construir um elastômero de desempenho para uso em um tênis de corrida que atenderia a todos os requisitos de durabilidade, etc.”
Os desafios da Carbon
A Carbon havia desenvolvido um avanço na impressão à base de resina que permitia a impressão de produtos em uma velocidade muito mais rápida – “reduzindo bastante as forças de adesão entre a parte de construção e a parte inferior do cassete, aproveitando a permeabilidade ao oxigênio de certos materiais – o oxigênio pode extinguir a polimerização nessa interface e fornecer forças de adesão muito mais baixas.”
A Carbon percebeu que “estávamos meio que nessa caixa de materiais curáveis por UV e materiais curáveis por UV tradicionais” – materiais provenientes das indústrias de revestimentos e impressão a jato de tinta, que não foram projetados para uso como materiais de desempenho para tênis de corrida ou aplicações automotivas.
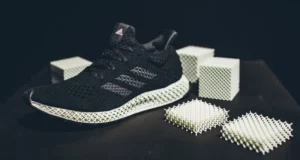
“E assim desenvolvemos esta plataforma de materiais de cura dupla – para expandir a paleta de materiais no espaço de formulação para que pudéssemos alcançar as propriedades necessárias. E, o que quero dizer com isso é, basicamente, temos resinas curáveis por UV que reagem com a luz UV e solidificam com a luz UV, e então temos resinas curáveis termicamente. As pessoas estão familiarizadas com isso quando você vai à loja de ferragens e compra uma resina epóxi de dois componentes, ou uma resina de silicone de dois componentes, ou uma resina de poliuretano de dois componentes.”
“Podemos pegar essas químicas e misturar a química UV com a química termicamente curável e depois misturá-las antes de entrar na impressora. Em seguida, usamos a impressora para solidificar a peça através da química UV. Então, formamos uma rede inicial com a impressão UV e basicamente prendemos essa química térmica nessa parte. E então tiramos a peça da impressora, limpamos e então ela vai para um forno onde você agora ativa aquela química termicamente curável que agora está incorporada em sua impressão inicial.”
Gen One
Este material inicial ‘Gen One‘ é o que Carbon usou para lançar os tênis Future Craft 4D com a Adidas, em 2017. E embora o material atendesse a todos os requisitos de durabilidade, estabilidade UV, estabilidade hidráulica, cor, velocidade de impressão, etc. sapatos eram mais pesados do que o desejado. A Carbon também queria se afastar da linha Originals da Adidas (uma linha de produtos focada mais em estilo de vida, novidade e ‘coolness’) e em direção ao lado de desempenho dos negócios da Adidas – para aprimorar os produtos e “levar para o próximo nível ”.
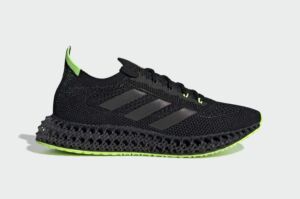
Se isso acontecesse, Carbon percebeu a necessidade de um material ‘Gen Two’ – um material que se tornaria EPU 44. Dos vários problemas que Carbon estava tentando resolver, um era que “para tirar o peso do sapato …. uma maneira de fazer isso é tornar os suportes da treliça mais finos, mas isso torna o sapato mais macio. E assim, você precisa de um material mais rígido que possa compensar essa redução no tamanho do suporte. Então, precisamos fazer um elastômero mais rígido que também tenha um alto retorno de energia e alta durabilidade, e todos esses requisitos para fazer um produto de desempenho.”
A segunda coisa é a propriedade conhecida como “força verde” – quando, no processo de cura dupla, a peça acaba de ser impressa, e só foi ativada pela rede UV. “O material nesse estado verde tem um conjunto de propriedades mecânicas que são importantes para ditar quais tipos de geometrias você pode imprimir. Quanto mais rígido você puder tornar esse material no estado verde – mais fácil será fazer algumas dessas geometrias de treliça mais complexas.”
Ao resumir aproximadamente cinco anos de trabalho, James Rolland explicou como a Adidas teve um conceito de um tênis de corrida de deslocamento para frente. Que era, essencialmente, uma treliça capaz de converter a força vertical em movimento horizontal – dando um pequeno pulso de dois milímetros ou mais de movimento para frente a cada passo. A Carbon trabalhou em estreita colaboração com a Adidas por aproximadamente três anos para garantir que o material ‘Gen Two‘ atendesse a todos os requisitos.
A Adidas fez um teste, quando o Boost, uma sola de espuma feita de poliuretano termoplástico expandido (eTPU), foi lançada – a Adidas colocou à prova soltando uma bola de aço sobre esteiras planas da espuma, na tentativa de provar as propriedades físicas da espuma. Quando caiu, a bola quicou mais alto do que sem a espuma – provando que o material forneceu um maior retorno de energia. Quando a Adidas repetiu o teste, com tapetes planos de EUP 44, a bola realmente quicou para frente, levemente.
Outro problema foi o da sustentabilidade – uma área onde tanto a Carbon quanto a Adidas se alinharam. Alguns dos projetos anteriores focados em sustentabilidade da Adidas incluem a linha Parley da empresa – onde a empresa usou plástico reciclado oceânico para fiar fios de poliéster – e os tênis de corrida totalmente recicláveis ’feitos para serem refeitos’, feitos totalmente de materiais recicláveis.
Felizmente, o uso desse polímero de origem biológica para EPU 44 resultou em uma viscosidade muito menor da resina – reduzindo o tempo de impressão e tornando a produção mais econômica.
“Foi um daqueles momentos em que os requisitos de sustentabilidade estavam alinhados com os incentivos econômicos e os incentivos de desempenho. E então tomamos a decisão de usar esse material bioderivado em nosso produto e, sim, funcionou muito bem.”
Graças ao desenvolvimento da EPU 44, a Carbon conseguiu aumentar significativamente a velocidade de impressão das solas impressas da Adidas. Jason Rolland também observou que “o material ‘Gen One‘ não tinha a força verde certa para realmente imprimir esses novos tipos de treliças. Ver a ciência de materiais avançando cada vez em direção à sustentabilidade é empolgante e satisfatório, para saber mais sobre esse projeto leia a matéria completa no site.
Para continuar por dentro das principais novidades do mundo da indústria acesse o nosso site.