A Manufatura Digital é um termo muito utilizado hoje em dia. Mas, qual o seu significado e como as empresas a estão aproveitando isto a seu favor?
Pode-se dizer que a Manufatura Digital é quando uma empresa aproveita as tecnologias digitais para beneficiar suas operações de manufatura. Com a Manufatura Digital, os fabricantes podem criar uma fábrica que é um ambiente conectado e totalmente integrado, permitindo-lhes usar análise de dados em tempo real para otimizar todo o processo de manufatura e obter ganhos de produtividade.
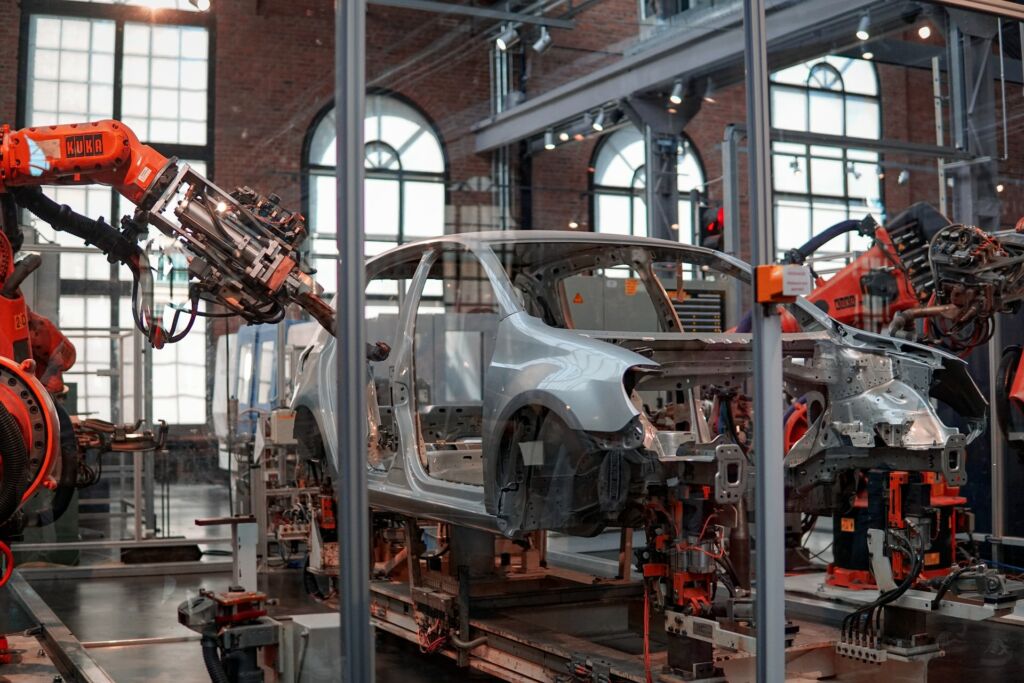
Dessa forma, a Manufatura Digital permite que os fabricantes eliminem gargalos, reduzam o estoque, melhorem a qualidade do produto/processo, diminuam o tempo de colocação no mercado, façam alterações rapidamente para atender às necessidades do cliente e expandam o número de produtos fabricados. Os investimentos da fábrica digital levaram a um aumento médio de 10% na produção, 11% na utilização da capacidade da fábrica e 12% na produtividade do trabalho, de acordo com a Deloitte.
Um resultado claro desta mudança é que a adoção de iniciativas de fábricas inteligentes pode ajudar os fabricantes dos EUA a triplicar a taxa de produtividade do trabalho até 2030, em comparação com as taxas lentas de 2007-2018, conforme dados apresentados pela Deloitte.
Problemas e pessoas primeiro
Antes de adotar qualquer tecnologia de Manufatura Digital, os fabricantes devem determinar o problema de negócios, como produção mais eficiente ou tempo de entrada no mercado mais rápido, que estão tentando resolver. Em seguida, defina metas mensuráveis e incrementais para o ROI. Alguns pioneiros compraram a tecnologia de fábrica digital com apenas uma vaga ideia do que queriam fazer, mas fracassaram.
As pessoas são a próxima prioridade. Um líder forte e visionário que entende a manufatura digital manterá os programas da fábrica digital avançando. Acima desse líder, o conselho também precisa estar engajado e educado sobre os benefícios. Abaixo desse líder, ouvir os funcionários da linha de frente sobre suas tarefas de trabalho, gargalos e expectativas fará a diferença entre a tecnologia que melhora os resultados financeiros ou fica abandonada em um canto.
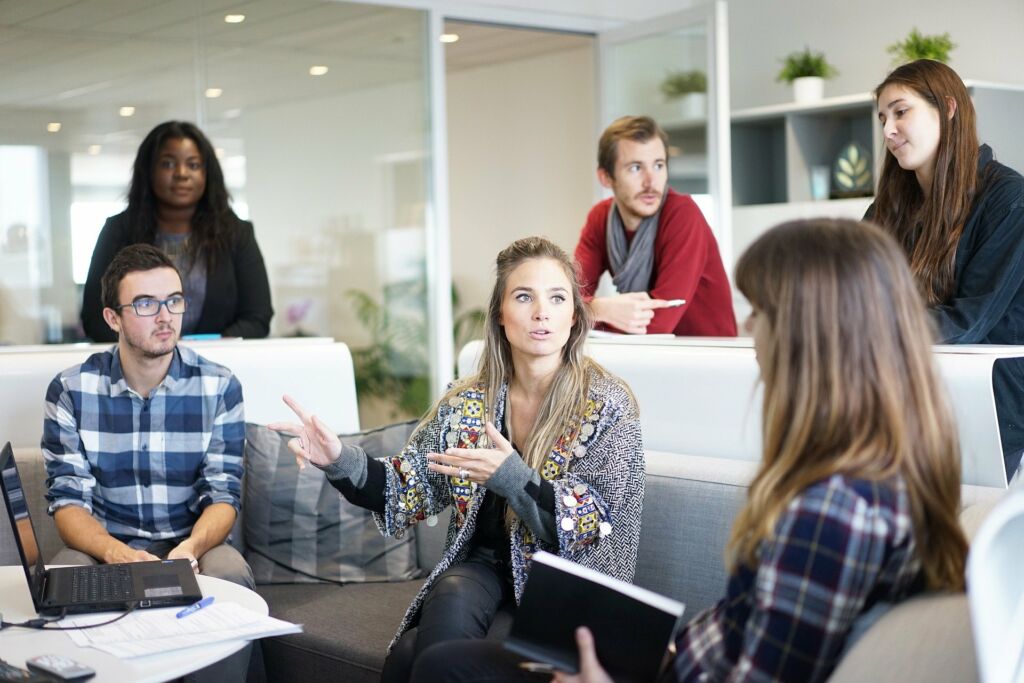
Estudos de caso da manufatura digital
De acordo com a Deloitte e outras empresas de consultoria, os casos de uso para iniciativas de manufatura digital incluem:
- Manutenção preditiva para evitar quebras dispendiosas;
- Sensoriamento e detecção de qualidade para monitorar e testar equipamentos e produtos em tempo real com análise visual;
- Eficiência preditiva para evitar gargalos dispendiosos;
- Monitoramento de temperatura para fazer os ajustes necessários nas ferramentas de corte para temperaturas mais altas;
- Otimização das estações de trabalho para beneficiar toda a linha de produção;
- Transporte inteligente para automatizar a movimentação de materiais, garantir o fluxo contínuo de materiais e eliminar backups;
- Colaboração de engenharia e gêmeo digital para prototipagem rápida, configuração de célula de produção virtual e modelagem de produto digital;
- Rastreamento de ativos em tempo real;
- A capacidade de ajustar a produção para atender às mudanças nas necessidades dos clientes e pedidos importantes.
A fábrica digital da Siemens é um forte exemplo de estudo de caso
A Siemens se destaca como grande realizadora. Em 2010, a empresa começou a digitalizar sua própria fábrica em Amberg, Alemanha. Na década seguinte, a fábrica evoluiu de 25% digital / automatizada para 75%. A produtividade aumentou em impressionantes 1.400%.
Antes da digitalização, a fábrica podia fabricar cinco produtos. Em um período de 12 meses, a fábrica estava em posição de fazer 1.300 produtos diferentes, com capacidade para fazer 9.000 no total, disse Alastair Orchard, vice-presidente de empresa digital da Siemens Digital Industries Software. Tempo do pedido à entrega: 24 horas.
Em vez de se concentrar apenas na otimização da produção em células de trabalho individuais, a fábrica digital da Siemens, e outras, tem uma visão ampla e longa para otimizar todo o processo ou até mesmo vários processos.
Como isso funciona: imagine que uma máquina da fábrica só pode fazer furos. Um robô de fábrica inteligente pode fazer furos, mas também pode soldar, executar alguns processos de montagem, selecionar e colocar componentes elétricos e testar componentes. Quando o trabalho do dia começa, o gêmeo digital determina a maneira mais eficiente de operar toda a fábrica e fabricar cada produto com base em todas as tarefas em mãos. Produtos idênticos podem ser produzidos usando diferentes combinações de células de trabalho de acordo com a carga de trabalho do dia inteiro, disse Orchard.
“Qualquer produto pode ir em qualquer jornada pela fábrica, interagindo com qualquer combinação de máquinas e pessoas”, disse Orchard. “O produto pode interagir com uma máquina, 10 máquinas, 15 máquinas. Introduzimos um paradigma completamente novo.”.
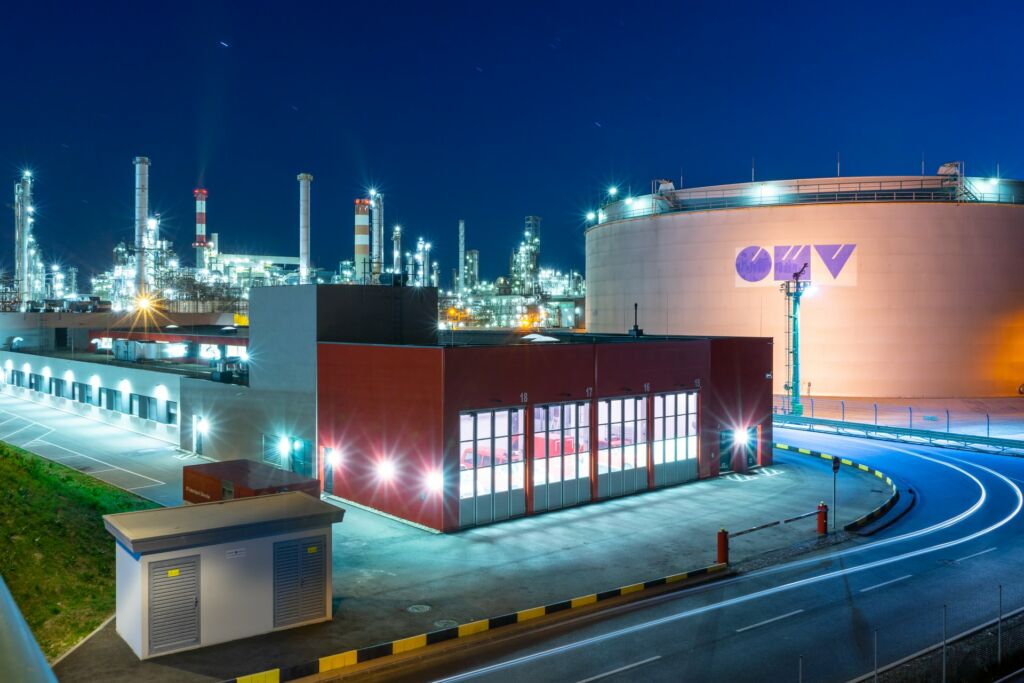
Os defeitos diminuíram, mas a velocidade também caiu
Os defeitos caíram de 150 por milhão para nove, disse Orchard. A melhoria inicial da qualidade veio às custas da velocidade, porque a fábrica fez um raio-X de todos os produtos para procurar componentes ausentes e defeitos de solda.
“Essa foi uma parte crítica do processo, mas retardou tudo”, disse Orchard. “Estávamos tentando fazer algo a cada segundo. Os raios X estavam consumindo uma quantidade considerável de tempo. Foi um gargalo enorme.”
Mas a Siemens não estava disposta a sacrificar a qualidade. Em vez disso, a empresa decidiu ser inteligente sobre quais peças radiografar.
A Siemens usou análise de dados para examinar os conjuntos de dados de 30 milhões que a fábrica tinha de peças radiografadas no passado. A empresa também analisou cerca de 200 fatores, como fornecedor, máquinas usadas, operadores específicos envolvidos, temperatura, umidade, informações de manutenção das máquinas e muito mais.
“Conseguimos treinar um algoritmo de aprendizado de máquina e prever com base em todos os valores coletados se haveria ou não problemas de qualidade”, disse Orchard. “Não fazemos raio-X de nada agora, a menos que o algoritmo de aprendizado de máquina diga que há mais do que uma pequena chance de este produto falhar. Removemos o gargalo. Somos capazes de operar a fábrica em velocidade total e fazer raios-X apenas nos poucos itens considerados como potencialmente com problemas. Conseguimos equilibrar qualidade e produtividade. ”
Os gêmeos digitais desempenham um papel importante nas fábricas digitais
Por fim, os gêmeos digitais também desempenham um papel na otimização da produção. Para empresas como a Siemens, que fazem e usam plataformas de fábrica digital, um gêmeo digital pode facilmente mostrar aos clientes o que a tecnologia pode fazer por eles.
Um funcionário da Siemens descreveu o gêmeo digital como dando a ele “a fábrica em seu bolso”.
A Siemens também está empurrando as iniciativas de manufatura digital de volta à linha de seus fornecedores. Quando a fábrica tinha problemas continuamente com os contatos em seus carrinhos inteligentes, a empresa incentivou seu fornecedor a usar a plataforma de conectividade inteligente da Siemens para coletar dados e vender um serviço de manutenção para a fábrica. Quando os contatos começam a falhar, mesmo que ligeiramente, o sistema aciona uma ação para enviar o buggy para uma estação de limpeza, em vez de interromper uma linha de produção inteira.
Ao buscar licitações para máquinas para esta fábrica digital, a Siemens insiste que seus fornecedores licitem por meio de um gêmeo digital. “Cada fornecedor volta para nós com um modelo digital funcional de uma máquina. Podemos vê-lo fazendo seu trabalho. Podemos prever o torque, o uso de energia, os intervalos de manutenção – tudo isso no mundo virtual. Escolhemos a melhor máquina, não no papel, mas nestas previsões muito detalhadas. ”
A Siemens obtém o gêmeo digital de uma nova máquina cerca de um mês antes de obter a máquina real e comissiona virtualmente o gêmeo digital para testar a produção. Quando a máquina real chega, a fábrica precisa de apenas 40 minutos para iniciar a produção total.
“Podemos ligá-lo e está pronto para funcionar”, disse ele.
Retardatários se preocupam com os riscos e desafios da fabricação digital
Apesar das vantagens claras da tecnologia de fábrica digital, 49% dos fabricantes americanos continuam presos no modo caneta e papel, de acordo com a Deloitte. Se eles usam análise de dados, as informações podem ter meses atrás.
Existem razões para essa relutância. Os executivos se preocupam em cometer erros que interrompam as linhas de produção; eles também se preocupam com violações de segurança. Esses temores legítimos ajudam a explicar por que 19% dos entrevistados da Deloitte nem mesmo estão pensando na transformação da fábrica digital e 30% estão pensando na ideia, mas não planejam seguir em frente.
Os primeiros usuários abriram caminho
Mas há boas notícias para aqueles que ainda não embarcaram na transformação da fábrica digital:
- Os primeiros usuários já identificaram pontos de estresse e falhas comuns. (Lembra-se do fracasso rápido da GE?) Agora, os que chegaram mais tarde podem aprender com essas lições.
- O custo das plataformas digitais está caindo. O software de fábrica digital agora é possível até mesmo para lojas menores.
- A tecnologia de fábrica digital é mais facilmente integrada entre os fornecedores. Os fornecedores entendem que os fabricantes não podem eliminar e substituir tudo em suas lojas, portanto, estão fazendo com que suas plataformas funcionem bem com a tecnologia existente.
Avalie cuidadosamente e trate dos riscos de segurança
Mas os riscos, especialmente os riscos cibernéticos das fábricas digitais, continuam sendo atraentes. Antes de prosseguir, os fabricantes devem avaliar cuidadosamente os desafios e riscos. Uma plataforma de segurança totalmente integrada pode aproveitar as vantagens da análise de dados em tempo real para combater os atores das ameaças cibernéticas. Uma abordagem inteligente para avaliar o risco, de acordo com a Deloitte:
- Avalie todas as novas tecnologias digitais com base na segurança humana.
- Ao conectar a fábrica e seus ativos à rede de comunicações mais ampla, implemente um plano de mitigação de risco ágil e em evolução.
- Evite falhas de ponto único segmentando a linha de produção e tendo mais de um canal de rede.
- Crie políticas padrão para recuperação de risco e desastre em todos os fornecedores que fornecem equipamentos conectados.
- Considere uma abordagem de segurança em camadas para fortalecer a resiliência.
Com todas estas mudanças, a forma de trabalho e novos postos também serão reorganizados. Confira no post O Futuro do Trabalho na Manufatura sobre isto!
Texto adaptado de What is digital manufacturing?