Não há mais repetidas fixações, o que leva a reduções nos tempos de set-up e maior precisão. Estes são dois benefícios que a AHP Merkle, fabricante de sistemas hidráulicos, vem colhendo desde a introdução de equipamentos de produção altamente automatizados. No coração da planta estão dois centros de usinagem horizontais fabricados pela Grob e equipados com um sistema de eixo U KOMtronic da Ceratizit para usinagem completa.
Na indústria de produção de ferramentais e matrizes, o nome AHP Merkle é sinônimo de cilindros hidráulicos duráveis e de alta qualidade – e não apenas na Alemanha. Fundada há cerca de 50 anos como operação com uma só pessoa, a empresa familiar tornou-se uma companhia de médio porte com atuação global.
Os cilindros hidráulicos, porém, são fabricados apenas na sede da empresa em Gottenheim, na Alemanha. Com uma nova unidade fabril, construída em 2010 e ampliada em 2014 e 2019, a empresa otimizou suas operações logísticas e produtivas. “Sempre tivemos a qualidade de nossos produtos em mente ao fazer todas as mudanças”, enfatiza Günther Reich, da equipe de Compras Técnicas. Em seus mais de 33 anos na empresa como especialista em usinagem, ele não apenas operou e programou máquinas, mas também foi posteriormente responsável pela introdução de máquinas CNC para torneamento e fresamento.
Nos últimos anos, Reich esteve fortemente envolvido na reestruturação do departamento de produção. “Na produção de ferramentais e matrizes – nosso principal setor em termos de clientes – há uma pressão significativa sobre os preços, o que tem um efeito indireto sobre os fornecedores de componentes”, explica Reich. “Nossos produtos, que oferecemos tanto como modelos padrão de estoque quanto em versões personalizadas, também são afetados. Como não economizamos em qualidade, os conceitos de máquinas e automação de última geração são de vital importância para nós.”
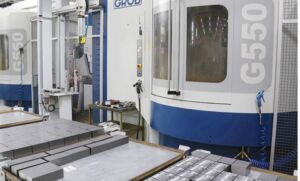
Reich refere-se ao equipamento para usinagem automatizada de cilindros de bloco em vários tamanhos e projetos a partir de uma quantidade. Para Reich, esses equipamentos representam um marco na área de produção da AHP, que basicamente consiste de dois centros de usinagem Grob G551 e um sistema de automação de páletes Promot. O processo, porém, começa muito antes, na programação das operações, onde as ordens de produção são planejadas e transferidas para a serra circular Kasto totalmente automatizada por meio do sistema ERP. É aqui que são produzidas as peças brutas feitas de barra cilíndrica C45 e armazenadas em um pálete especial com a ajuda de um robô.
Ao mesmo tempo, o software gera um arquivo contendo todas as informações do pedido, desde a posição exata de cada peça bruta no pálete, comprimento, quantidade e número do artigo, até o programa CNC, para posterior processamento no centro de usinagem. Por fim, um código de barras impresso acompanha o pálete até a área de carregamento no sistema Promot, que o aloca em um local livre e são inseridos todos os dados por meio do código de barras.
“Mesmo em uma linha de produção automatizada, as funções são desafiadoras e variadas”, explica Günther Reich. “Não tem nada a ver com simplesmente apertar botões.”
Merkle-Oliver-Scheppele-Komplettbediener
Scheppele é um dos funcionários de produção treinados e motivados da AHP Merkle. Ele opera todo o sistema Grob/Promot e também estava envolvido no processo de aquisição. “Quando estávamos planejando a planta em 2015 – na época usando apenas um centro de usinagem Grob G551 – nosso objetivo principal era ser capaz de usinar completamente as caixas de cilindro em apenas um set-up”, diz o especialista em usinagem.
“Queríamos usá-lo para minimizar os tempos de set-up e melhorar ainda mais a qualidade. Além disso, precisávamos de algo que pudesse funcionar o mais próximo possível de 24 horas por dia, seis dias por semana, mesmo durante turnos sem operadores. Nisso é que baseamos os detalhes.”
TORNEAMENTO E USINAGEM
Scheppele se refere a equipar a fábrica com ferramentas e software. Afinal, carcaças de cilindros como as que sua empresa produz exigem várias operações de fresamento, mandrilamento e torneamento, que até então eram executadas em pelo menos duas máquinas e envolviam vários set-ups. É necessária uma ferramenta muito especial para poder realizar tudo isso no centro de usinagem horizontal com seus três eixos lineares e dois rotativos: um eixo U, como explica Günther Reich.
“A Ceratizit é um dos nossos parceiros de ferramentas. Há mais de 30 anos adquirimos várias ferramentas de furação e fresamento, pastilhas intercambiáveis e adaptadores. Depois de ver o sistema de eixo KOMtronic U-axis em sua fábrica em Besigheim em 2015, pensamos que seria a solução ideal para nossos processos de usinagem no centro de usinagem Grob, pois é mais flexível do que outras ferramentas especiais.”
Duas gerações do sistema de eixo U KOMtronic UAS-160 da Ceratizit são usadas na AHP Merkle. Não há diferença no manuseio e programação em comparação com as gerações anteriores, mas apresenta um funcionamento mais silencioso, resultando em vida útil da ferramenta de pastilhas intercambiáveis de cerca de 40 minutos a mais.
ETAPAS
A principal razão para isso é que os sistemas de eixo U KOMtronic livremente programáveis possibilitam qualquer operação de contorno e torneamento em peças estacionárias não rotacionalmente simétricas. Combinado com ferramentas de encaixe feitas sob medida e pastilhas intercambiáveis selecionadas, tanto contornos em furos quanto usinagem externa podem ser executados. Os processos são mudados para o eixo U nas máquinas Grob.
Oliver Scheppele diz que, uma vez que o bloco foi pré-perfurado e cortado no comprimento, usa o sistema de eixo primeiro para virar o contorno do furo do cilindro, o furo central da rosca e o primeiro ajuste com chanfro.
Depois que esses processos de desbaste são realizados, a peça de trabalho é medida e os resultados da medição são usados para correção automatizada. Ajustes adicionais são realizados e a superfície do cilindro é laminada. “É assim que alcançamos a superfície ideal em termos de função de deslizamento e vedação”, diz Scheppele. “Depois do fresamento de roscas ser concluído, preciso do eixo U novamente para traçar o contorno ao longo dos chanfros, a fim de remover as rebarbas do processo de laminação e obter um arredondamento limpo. O eixo U KOMtronic é indispensável para esta tarefa.”
Posteriormente, é realizada a usinagem de furos para montagens e conexões, e uma verificação final dos ajustes é realizada com um apalpador. “O eixo U da Ceratizit nos permite usinar completamente 95 por cento de todas as carcaças de cilindros na Grob G551, evitando que tenhamos que fazer todo o retrabalho durante a montagem final”, resume Oliver Scheppele.
“Embora nossos cilindros hidráulicos sejam em geral componentes relativamente pequenos dentro de um sistema grande, eles ainda são importantes. Afinal, o sistema parará se um único cilindro vazar e falhar. O eixo U também é uma peça relativamente pequena, mas não poderíamos ficar sem ele”, observa Günther Reich. É por isso que o comprador solicitou um segundo sistema de eixo U como backup logo após o primeiro, acrescenta.
Quando a AHP Merkle expandiu sua fábrica em 2021 para incluir a segunda máquina Grob G551, eles colocaram dois dos mais recentes modelos de eixo U: o KOMtronic UAS-160-3 no formulário de pedido desde o início. “Não há diferença no manuseio e programação desta terceira geração em comparação com as versões anteriores, o que significa que nenhum novo treinamento foi necessário. As diferenças estão no funcionamento interno, resultando em um funcionamento ainda mais silencioso e nos permitindo aumento na vida útil da ferramenta de cerca de 40 minutos a mais para nossas pastilhas intercambiáveis”, afirma Oliver Scheppele.
CONFIABILIDADE
Para garantir a segurança do processo, crucial para um processo de produção automatizado, Scheppele insistiu em adquirir um processo de alto desempenho e uma ferramenta de monitoramento de colisão quando o primeiro G551 foi adquirido. Sua determinação foi recompensada na forma do sistema de monitoramento e controle ToolScope do fornecedor de ferramentas Ceratizit. O ToolScope, instalado no gabinete de controle do G551, registra continuamente o consumo de energia e outros sinais da máquina que são gerados durante o processo de produção. Esses dados são visualizados na tela de operação e usados para monitorar e ajustar a máquina.
“O monitoramento do ToolScope é de fácil set-up e muito eficaz. Tenho a opção de definir cada operação e definir certos limites em relação ao consumo de energia para cada ferramenta individual”, explica Scheppele.
“O sistema detecta o desgaste atual da ferramenta com base na força média do processo, para que eu possa trocar a ferramenta no momento ideal. Além disso, o ToolScope identifica quebras e colisões de ferramentas e aciona uma parada de emergência em menos de 1 ms. Isso reduz ao mínimo os danos resultantes à ferramenta, peça de trabalho e máquina. Já passamos por uma situação de emergência como esta. Felizmente, nenhum dano foi causado graças ao recurso de monitoramento de colisão do ToolScope”, conta o operador da máquina. Isso dá tranquilidade, especialmente quando o sistema roda sem operador.
O ToolScope possui recursos ainda mais úteis, como controle de avanço adaptativo, que acelera o processo onde é seguro fazê-lo e simultaneamente protege a ferramenta interceptando picos de carga. “Uso esse recurso há algum tempo ao fresar peças inclinadas, pois ele me permite evitar uma velocidade de corte variável. A ferramenta se beneficia de uma vida útil mais longa – é uma solução muito sofisticada”, acrescenta Scheppele.
APROVAÇÃO
Fica claro por que Günther Reich considera o sistema de produção automatizado um marco nas operações de produção da empresa: graças a este equipamento altamente automatizado, a AHP Merkle conseguiu reduzir o tempo de produção das carcaças dos cilindros de bloco em cerca de 40 por cento e implementar turnos sem operadores. O tempo médio de usinagem é de 19,2 horas por dia, um número notável para a operação individual pela qual Oliver Scheppele também é responsável.
Ele está satisfeito: “Produzimos aproximadamente 15.000 carcaças de cilindros de bloco ao longo do ano em uma única máquina. A adição da segunda Grob G551 deverá aumentar ainda mais esse número”, afirma. “As duas máquinas geralmente usinam cilindros de diferentes diâmetros, mas se uma delas falhar, não demorará muito a outra assuma as tarefas de sua contraparte.” Para saber mais acesse o site.
Para continuar por dentro das principais notícias do mundo da indústria acesse o nosso site.