A Aerojet Rocketdyne, com sede em Los Angeles – um fabricante com uma orgulhosa herança em voos espaciais e propulsão de foguetes – é um fornecedor importante de sistemas para a tão esperada missão Artemis da NASA (e da ESA), que deve trazer a humanidade de volta à Lua, desta vez ficar. A manufatura aditiva – e particularmente a tecnologia da Velo3D , também em uso na SpaceX – poderia ajudar a Aerojet Rocketdyne e a NASA a atingir seus objetivos de forma mais rápida e econômica.
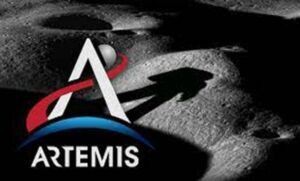
Esperançosamente, começando em 2022 (embora a missão já tenha sido adiada várias vezes), a NASA colocará a espaçonave não tripulada Orion na órbita lunar, seguida de pousos tripulados, construção de habitats lunares e infraestrutura de apoio e, finalmente, preparação para uma visita a Marte. De acordo com o administrador da NASA Jim Bridenstine, a agência espacial e seus parceiros vão conseguir isso até o final desta década e fazê-lo com metade do poder de compra que tinha em 1964, quando o desenvolvimento da Apollo estava no auge.
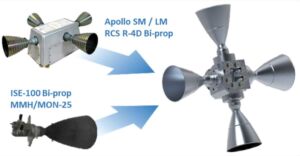
“Como em qualquer empreendimento complexo, quanto mais acessível você puder torná-lo, maior a chance de garantir sua conclusão, e a lua não é diferente”, disse James Horton, engenheiro aeroespacial e arquiteto de missão da Aerojet Rocketdyne. “A Metal AM desempenha um papel fundamental para atingir esses objetivos.”
Construindo um legado
Como uma empresa espacial pioneira, abrindo caminho para a indústria espacial comercial de hoje, a Aerojet Rocketdyne tem uma longa história em metal AM. Por mais de duas décadas, a empresa investiu muito tempo e recursos para alavancar essa importante tecnologia, concentrando a maior parte de suas energias na fusão em leito de pó a laser (LPBF). É devido a esses esforços que o fabricante aeroespacial conseguiu projetar e integrar com sucesso componentes de uso final impressos em 3D para uma variedade de projetos, entre eles os enormes motores RS-25 que levarão a missão Artemis ao espaço .
Horton esteve lá por muito disso. Desde 2008, ele ocupou cargos de liderança em projetos de motores de foguetes, desenvolvimento e operações de voo de teste para a NASA e o DOD. Sua equipe de propulsão avançada na Aerojet Rocketdyne está atualmente trabalhando em propulsão química, elétrica e nuclear para apoiar os esforços de exploração do espaço profundo da NASA, incluindo o projeto Artemis.
Ele lhe dirá que o metal AM, quando usado em conjunto com software avançado de design e simulação, oferece aos engenheiros aeroespaciais de hoje “um bufê inteiro de soluções que estavam completamente indisponíveis para seus antecessores, fornecendo a capacidade incomparável de inovar sem compromisso”. Por causa disso, a Aerojet Rocketdyne conseguiu reduzir os custos de propulsão, acelerar o tempo de lançamento no mercado e melhorar o desempenho de seus produtos como nunca antes.
Caso em questão
Um exemplo recente disso é um subsistema crítico que os engenheiros da Apollo conheciam como um sistema de controle de reação “quádruplo” (RCS). O Apollo RCS incluía quatro propulsores bipropulsores R-4D individuais, originalmente projetados pela Marquardt Corp., que usavam tetróxido de nitrogênio hipergólico (ignição espontânea) e hidrazina como propulsores.
Cada módulo de aterrissagem e serviço lunar tinha quatro quadriciclos, cada um dos quais gerava mais de 100 libras de empuxo para controlar a rolagem, inclinação e guinada da espaçonave durante o vôo. Após uma série de aquisições, a Aerojet Rocketdyne eventualmente assumiu a propriedade do R4-D, com a intenção de usar o que agora é chamado de “sistema de controle de reação” (RCS) na futura espaçonave.
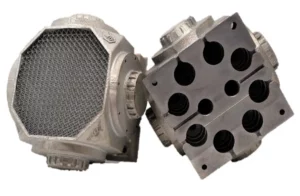
Dado que o projeto original do RCS tem mais de 60 anos, Horton e sua equipe reconheceram uma oportunidade de melhoria e iniciaram o que se tornaria um dos muitos projetos internos de pesquisa e desenvolvimento (IRAD) destinados a otimizar os sistemas necessários para o programa Artemis e outros projetos lunares comerciais. No caso do RCS, eles procuraram maneiras de reduzir o número de peças do motor, aumentar sua confiabilidade e facilitar a montagem e a manutenção, o que diminuiria os custos do projeto e melhoraria o desempenho da espaçonave. Metal AM marcou todas essas caixas.
“Durante todo o programa Apollo, a NASA produziu mais de 650 propulsores para apoiar seis pousos na Lua”, disse Horton. “Foi um número enorme, o que nos levou a acreditar que estávamos em algo grande – sabíamos que, se pudéssemos trazer acessibilidade ao RCS, poderíamos ter um impacto positivo em qualquer programa deste e futuros.”
Eles também queriam aproveitar os avanços de combustível de foguete. Como Horton explicou, os engenheiros de propulsão aprenderam ao longo dos anos que a adição de 25% de óxido nítrico ao oxidante de combustível mencionado anteriormente – tetróxido de nitrogênio – reduziria seu ponto de congelamento de -9 ° C (16 ° F) para -55 ° C (-67 °F). Como isso reduz o consumo de massa e energia dos sistemas de aquecimento necessários para evitar linhas de combustível congeladas no espaço, apresentou à Aerojet Rocketdyne uma oportunidade significativa. Havia apenas um problema: o combustível MON-25 que acabamos de descrever é instável, uma condição que Horton sugeriu ser uma “coisa ruim de se ter em foguetes”.
Provando o conceito
Aqui, novamente, o metal AM foi a resposta, pois permitiu que a equipe imprimisse geometrias especiais de injetores que poderiam queimar o combustível de maneira estável. Eles logo projetaram e construíram um modelo conceitual da superliga à base de níquel Inconel 718, mas infelizmente encontraram limitações com sua impressora 3D de metal.
“Tivemos que construir o corpo do injetor RCS em um ângulo de 45 graus, devido a preocupações com a saliência, e também adicionar uma série de grandes estruturas de suporte para evitar deformação térmica durante o processo de construção”, disse Horton. “Os suportes precisariam ser usinados posteriormente, adicionando custo ao produto, enquanto o ângulo de orientação criava uma qualidade de superfície inferior à desejável. Definitivamente, havia espaço para melhorias.”
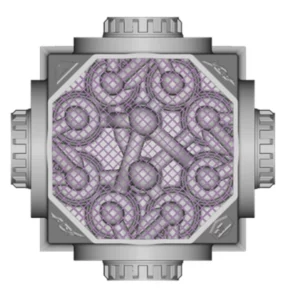
Ao mesmo tempo, eles perceberam que havia espaço para uma redução substancial de peso e otimização de topologia. Horton observou que eles eliminaram “grandes pedaços” de material desnecessário durante o redesenho, mas estava longe de ser perfeito. “Cada quilo de material que você pode remover de uma espaçonave economiza dinheiro nos custos de lançamento”, disse ele. “É por isso que recorremos à nTopology para obter ajuda na otimização do design e, em seguida, à Velo3D para construí-lo para nós.”
Descasque, preencha e imprima novamente
Técnicos da empresa de software de engenharia e design nTopology, com sede em Nova York, conseguiram rapidamente “descascar” a estrutura em blocos do corpo do injetor, deixando espessuras de parede consistentes ao redor das portas e canais de fluido complexos, eliminando áreas de concentração de tensão. Eles então preencheram o vazio resultante com uma estrutura de treliça fina, aumentando sua força e rigidez enquanto adicionavam apenas um peso mínimo; por causa de suas capacidades de “modelagem implícita”, nTopology foi capaz de cortar a massa do injetor quad pela metade.
A equipe da Aerojet Rocketdyne enviou o arquivo de peça otimizado para as instalações da Velo3D em Campbell, CA. Foi lá que o fornecedor de soluções de AM de metal deu a Horton boas notícias. Devido ao domínio da empresa em titânio impresso em 3D – um metal preferido em toda a indústria aeroespacial por sua resistência e leveza – o corpo do injetor RCS pesaria muito menos do que o Inconel. E como o engenheiro de vendas técnico da Velo3D, Gene Miller, observou, não haveria necessidade de construí-lo em um ângulo ou usar os grandes suportes em blocos como na primeira iteração.
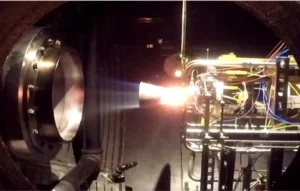
“Nosso software proprietário de pré-impressão é intuitivo o suficiente para reconhecer diferentes características geométricas e aplicar parâmetros específicos de laser a essas áreas para que imprimam da maneira mais eficiente possível e sem a necessidade de material de suporte adicional”, disse Miller. “Além disso, somos um dos poucos fornecedores de sistemas AM de metal que podem imprimir com sucesso peças grandes e complexas de titânio sem rachaduras. Temos uma solução exclusiva para mitigar o estresse interno acumulado no material impresso e podemos evitar rachaduras mais do que outras impressoras no mercado.”
Conclusão
O resultado final? A Aerojet Rocketdyne agora tem um propulsor RCS que tem 1/5 da massa, 1/2 do tamanho e 1/3 do custo de uma versão fabricada convencionalmente. E como contém muito menos componentes, também é mais fácil de montar, com muito menos chance de falha durante a operação.
Disse Horton: “Mostramos que, ao alavancar a manufatura aditiva e a tecnologia de software avançada, podemos incluir acessibilidade, reduzir os prazos de entrega e melhorar muito o desempenho do sistema em comparação com a forma como construímos as peças no passado. Nosso próximo passo é demonstrar essa prova de conceito, trazendo-a para testes de campo reais e, esperançosamente, para a qualificação final. De lá, ele vai para o espaço.” Sem dúvidas o uso da manufatura aditiva trouxe grandes benefícios para a missão, para saber mais acesse o site.
Para continuar por dentro das principais novidades do mundo da manufatura aditiva acesse o nosso site.