Conforme a simulação virtual avança, a inovação fica mais rápida e menos custosa. A tecnologia de simulação (como por exemplo a SDfM – Simulation-Driven Design for Manufacturing) avança continuamente para modelar o comportamento do produto cada vez mais no mundo real, no entanto, muitas empresas ficam para trás em sua adoção.
Uma pesquisa recente descobriu que apenas 37% dos entrevistados disseram que aplicaram simulação de fabricação durante a fase de design do produto. A grande maioria estava verificando a capacidade de fabricação do produto apenas depois que o projeto foi concluído. Às vezes, a simulação era usada ainda mais tarde, após a ocorrência de uma falha no produto. A falta de adoção de design orientado por simulação para manufatura (SDfM) geralmente se deve às preocupações com os custos da empresa e à falta de treinamento e recursos, apesar dos gerentes estarem cientes de suas vantagens.
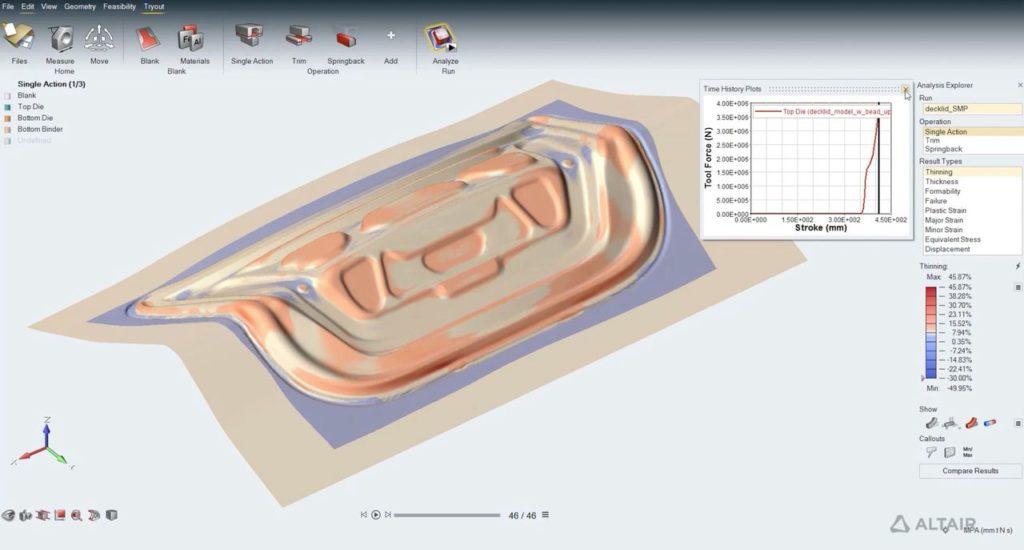
SDfM: o que as empresas estão perdendo
No entanto, ao evitar o SDfM, as empresas estão perdendo a capacidade de reduzir os custos de fabricação do produto, otimizar o processo de design, aumentar os cronogramas de produção e entregar produtos aos clientes com mais eficiência. Essas vantagens que o SDfM oferece surgem em meio à crescente complexidade do produto e à demanda do consumidor por intervalos mais rápidos de lançamento no mercado.
“A capacidade de fabricação de um produto pode afetar muito o custo”, disse o vice-presidente de marketing da Altair, Simone Bonino, que falou ao lado de outros apresentadores no evento Future.Industry 2021 em outubro. “Se você está simulando cedo e frequentemente, está realmente acelerando o design. É aí que você vê o valor de um projeto orientado por simulação para a abordagem de capacidade de fabricação. Ele permite um design generativo para todos os processos de fabricação com facilidade. Ele permite que você analise montagens complexas com grande precisão. E otimiza o projeto para capacidade de fabricação, selecionando o melhor processo antecipadamente.”
Bonino disse que Altair começou a introduzir o conceito de design orientado por simulação há quase duas décadas. Hoje, as soluções SDfM cobrem uma ampla gama de processos como impressão 3D, fundição, conformação de metal, moldagem por injeção, extrusão, fabricação de processo, formação de poliuretano, placas de circuito e eletrônicos e compostos – cada um com um produto de software diferente para permitir a simulação especializada, como o recém-lançado Inspire Mold para moldagem por injeção e o Inspire PolyFoam para formação de poliuretano.
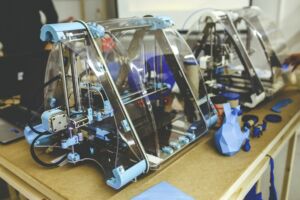
Além disso, os engenheiros podem utilizar o Centro de dados de materiais Altair para pesquisar ou navegar por materiais, visualizar propriedades de materiais, comparar tipos de materiais e obter ajuda para escolher o software de simulação relevante e exportar arquivos de dados de simulação.
Ao começar bem no início do ciclo de desenvolvimento, uma variedade de produtos é adequada para simulação. Além disso, usar o SDfM como uma primeira etapa no processo resulta em melhor desempenho e capacidade de fabricação porque a colaboração da equipe, avaliação e convergência rápida ainda são possíveis, disse Bonino. A tecnologia também permite a avaliação do desempenho físico simples e acoplado, podendo ser usada para gerar designs originais para produtos inovadores e fornece maiores percepções sobre o processo de fabricação geral.
Potencial do SDfM
Para ilustrar o potencial do SDfM, a engenheira de aplicação da Altair, Chen Meng, falou sobre a previsão da viabilidade de fabricação de peças de chapa metálica usando métodos virtuais. Ela começou com um exemplo de uma peça de suporte de bateria de metal. O objetivo era otimizar o suporte para manter os requisitos de desempenho mesmo em cenários extremos, como 3,6 Gs de carga aplicada à peça em um cenário de frenagem brusca. Além disso, outras restrições foram definidas para as condições de maximizar a rigidez e a otimização, como a aplicação de não mais do que 50 MPa de tensão e tendo o primeiro modo de flexão maior do que 85 Hz.
Em vez de conduzir um processo físico de tentativa e erro para fabricar um suporte de bateria que atenda aos objetivos declarados, Meng defendeu a realização de uma simulação sistêmica para verificar a viabilidade de fabricação durante o processo de design para criar um produto de alto desempenho e manufaturável, economizando tempo e custos em o ciclo de desenvolvimento.
O processo de fabricação da folha de metal envolve fases de formação onde uma folha de metal plana é transformada no produto final em várias etapas. Geralmente, o processo começa com um esboço de linha de base do projeto, otimização do projeto, interpretação do projeto, análise de viabilidade de fabricação e validação rápida – tudo resultando em produtos de alto desempenho e manufaturáveis.
O modo como os materiais se comportam durante o processo de conformação determinará se a peça pode ser fabricada. O comportamento é revelado por meio de dados de tensão baseados nas propriedades mecânicas dos materiais medidos em ensaios de tração. Por exemplo, quando uma máquina estica uma folha, a deformação é inicialmente elástica e reversível; no entanto, a alteração pode se tornar irreversível se a folha for estendida ainda mais. Finalmente, o estiramento extremo pode causar a quebra da folha.
Os testes de material podem determinar o limite de deformação que leva aos três defeitos de fabricação mais comuns durante a conformação de chapas: rachaduras, retorno elástico e defeitos de superfície. As divisões ocorrem quando o material é empurrado além de seus limites e fica esticado ou quebrado. Ao mesmo tempo, os defeitos de retorno elástico são causados principalmente por imperfeições no comportamento das qualidades elásticas do material. Finalmente, os defeitos superficiais incluem marcas ligeiramente côncavas ou convexas. Os defeitos de superfície são especialmente relevantes para peças externas, como portas de carros e são causados por vários problemas, como muita pressão aplicada à peça ou má aplicação de ferramentas durante o processo.
O processo de design tradicional depende de tentativa e erro e corrige os defeitos com ferramentas e alterações de design até que o produto seja fabricado. No entanto, o redesenho e a reconstrução de ferramentas são processos demorados e caros. Por outro lado, o uso de simulações virtuais para prever o resultado das fases de formação pode agilizar o processo. Para entender mais sobre o processo e suas características leia a matéria completa no site.
Para continuar aprendendo sobre os principais conteúdos da indústria 4.0 leia o nosso site.